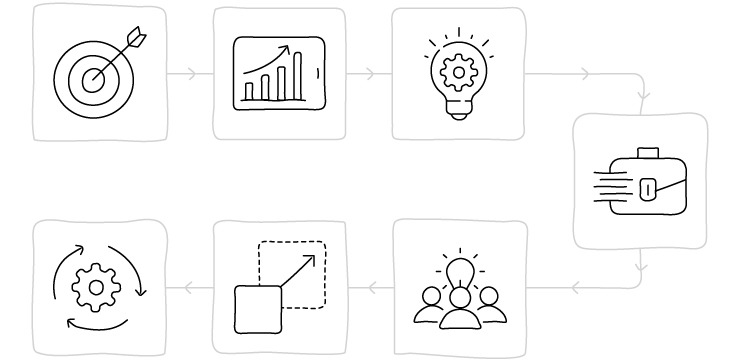
Introduction
Digital transformation is reshaping industries worldwide, and manufacturing is no exception. Integrating digital technologies into manufacturing processes has become crucial as businesses strive for greater efficiency, productivity, and innovation. From automating processes to optimizing supply chains and improving product quality, digital transformation in manufacturing is reshaping how companies operate.
In this step-by-step guide, we will explore the critical stages of digital transformation in manufacturing and how can companies use it to stay competitive? Read the blog to learn the benefits and how to implement it to advance the operations.
What is Digital Transformation in Manufacturing?
Digital transformation in manufacturing refers to using technology to improve business performance by increasing revenue, cutting costs, enhancing product quality, and boosting flexibility. This transformation can involve various processes, such as improving asset management, increasing workforce efficiency, and speeding up production.
Manufacturers can make smarter decisions, streamline operations, and create better products faster by adopting digital tools and technologies like IoT, automation, and data analytics. Ultimately, digital transformation helps companies stay competitive and adapt to changing market demands while creating new opportunities for growth and innovation.
Some examples are robotic process automation (RPA), mobile apps to manage workers on the frontlines, 3D printing, ERP systems, and automating tasks that require knowledge work.
Why is Digital Transformation Important?
The manufacturing industry is facing big challenges, like rising costs and the need to be more eco-friendly. To stay competitive, companies must use new technologies to work faster, waste less, and keep up with customer demands.
In fact, research shows that companies worldwide will spend over $3.9 trillion on digital transformation by 2027, with many manufacturing businesses leading the way.
The main reason for this change is to stay ahead of the competition. Most business leaders agree that using digital technology is very important for success. So now, the question is not if companies should use digital tools, but how they can do it the right way.
Digital transformation also brings many new opportunities. It helps companies produce more, improve the quality of products, and deliver goods faster. Businesses can also make better decisions using data, boost worker productivity, and keep machines running longer without breaking down.
Benefits of Digital Transformation in Manufacturing
There are many good things that happen when a manufacturing company embraces digital transformation. Let’s look at a few of the most important benefits:
1. Enhanced Efficiency
One of the biggest goals of digital transformation is to help factories work faster and more efficiently. Robots and AI-powered machines can do simple, repetitive tasks, which frees up workers to focus on more important jobs. With real-time data and monitoring, companies can make quick decisions, reduce downtime, and keep production running smoothly.
2. Better Product Quality
Digital tools can also help improve the quality of products. Sensors and AI can monitor production lines in real time, catching problems before they turn into big issues. This helps ensure that every product meets high standards, reduces the need to fix mistakes, and lowers costs. It’s also good for the environment because less waste is produced.
3. Safer Workplaces
Safety is very important in factories, and new technology is helping to make workplaces safer. Tools like augmented reality (AR) can give workers step-by-step instructions to complete tasks safely, reducing accidents. Real-time monitoring systems can also spot hazards, like machines that are about to break, and alert workers before something bad happens.
4. Greater Flexibility and Agility
In today’s world, the manufacturing industry is changing quickly. There’s more demand for different products, and products don’t stay popular for long. Digital transformation in manufacturing helps companies become more flexible. This means they can quickly change how they make things and manage their supply chains better. When companies can quickly adjust to market changes, they stay competitive in a fast-moving world.
5. Better Customer Experiences
Digital technologies also help companies give better service to their customers. This includes faster delivery times, higher-quality products, and services that are more personalized. For example, manufacturers can use information from smart products to predict when something might break. This way, customers can fix things before they break, saving them money. By focusing on what customers need, manufacturers can build stronger relationships and make customers happier.
Step-by-Step Guide to Implementing Digital Transformation in Manufacturing
Now that we know the benefits of digital transformation, let’s look at how companies can make it happen. Here’s a simple guide for businesses that want to start using digital transformation.
Step 1: Define Your Goals and Objectives
Before starting, it’s important to know what you want to achieve. Do you want to make your operations more efficient? Cut costs? Improve product quality? Or make customers happier? By setting clear goals, you’ll know exactly what your digital transformation efforts should aim for.
Step 2: Assess Your Current Digital Maturity
Next, take a close look at your company’s current digital abilities. This means checking if your technology, processes, and skills are up to date. Many companies still use older systems that slow down their progress, so it’s important to see what needs to be updated or replaced.
Step 3: Develop a Digital Transformation Strategy
Once you know your goals and where you stand, you can create a plan. This plan should explain what technology and changes are needed to meet your goals. It’s important to include everyone—like managers, IT staff, and other workers—so everyone is on the same page.
Step 4: Start Small with Pilot Projects
It’s a good idea to start with a small project. For example, you could add sensors to a production line or use data to manage your inventory better. This way, you can see how digital transformation works and make any changes before going bigger.
Step 5: Invest in Employee Training and Change Management
Digital transformation is not just about technology—it’s also about changing how people work. It’s important to train employees so they understand the new systems and how it will affect their daily tasks. Providing training helps them feel ready for the changes.
Step 6: Scale Up and Integrate Across the Organization
After testing your small project, you can expand it to other areas of the business. This could mean adding more smart technology to different parts of production or automating more tasks. Keep track of how things are going and see how the changes are helping you reach your goals.
Step 7: Continuously Evaluate and Adapt
Digital transformation is a long-term process, not something you do once and forget. As new technologies come out and the market changes, you’ll need to keep checking how things are going. This might mean updating your strategy or trying new technologies to stay on track.
Challenges of Digital Transformation in Manufacturing
Digital transformation in manufacturing brings many benefits, but it’s not always easy. Manufacturers face several challenges along the way. Let’s explore some of these obstacles.
1. Getting Everyone on the Same Page
Many manufacturers have trouble making sure their digital transformation plan matches their overall business goals. If the digital changes don’t align with the company’s main objectives, things can get confusing and inefficient. It’s important for manufacturers to connect their digital efforts with what they want to achieve as a company.
2. Managing and Connecting Data
Data is a big part of digital transformation, but it can be hard for manufacturers to manage all the information. Sometimes, data is stored in different places and it’s difficult to get a clear picture. To fix this, manufacturers need a plan to make sure the data is accurate, easy to access, and can be used by everyone in the company.
3. Getting Employees to Support Change
For digital transformation to work, all employees need to support it. But change is hard for many people, and some may resist it. Manufacturers need to teach their employees about the benefits of digital transformation and make sure they have the skills to succeed in the new digital world.
4. Finding the Right Technology Partner
Digital transformation often needs outside help from technology experts. It’s important for manufacturers to find the right partner to help them implement digital solutions. The right partner will provide the right tools and support to make sure the transformation is successful and can continue to grow with the company.
5. Managing Change Effectively
Successful digital transformation also requires good change management. Companies need leaders who can manage the changes, make sure things are on track, and ensure that the digital efforts help the company reach its business goals.
Real-World Examples of Digital Transformation in Manufacturing
Let’s look at some companies that have used digital transformation to improve their manufacturing.
1. Siemens: Smart Factories and IoT
Siemens is a big name in electronics and automation. They have created smart factories that use Internet of Things (IoT) sensors to gather data from the production line. This helps Siemens make quick adjustments and predict problems before they happen. By using this technology, they have improved productivity and reduced errors.
2. General Electric (GE): Predictive Maintenance with AI
GE uses Artificial Intelligence (AI) to predict when machines might break down. Their Predix platform collects data from machines and analyzes it to figure out when they need maintenance. This helps GE save money and reduce downtime, making their operations more efficient.
3. Tesla: Advanced Automation and Robotics
Tesla uses robots and automation to help with tasks like welding, assembly, and painting at their Gigafactory. By automating parts of the production process, Tesla has been able to make more cars while keeping quality high. They also use real-time data to continuously improve their processes and reduce waste.
4. Caterpillar: Big Data and IoT
Caterpillar, which makes construction and mining equipment, uses IoT sensors to gather data about how their machines perform. This helps them provide maintenance services to their customers and keep their equipment running smoothly. They also offer tools that let customers track and manage their machines remotely.
5. Boeing: Augmented Reality for Assembly
Boeing, the largest maker of airplanes, uses augmented reality (AR) to help workers put planes together. AR headsets show digital instructions on real parts, which helps workers do their jobs faster and with fewer mistakes. This has helped Boeing reduce production time and improve safety.
Final Thoughts
Digital transformation is no longer a trend but a necessity for manufacturing companies aiming to stay ahead. Manufacturers can streamline operations, reduce costs, enhance product quality, and improve customer satisfaction by following a structured approach to adopting cutting-edge technologies. While the journey to digital transformation may seem complex, taking it step by step ensures that the process is manageable and impactful. Manufacturers need to align their digital efforts with their business goals, manage data well, support employees, and find the right partners. By following these steps, manufacturers can make their digital transformation a success and be ready for the future.